1、Process features
1.1The average of product purity is more than 91%, the rate of superior product is more than 80%, and the rate of first-class products is more than 90%.
1.2The process belongs to the sixth generation of sodium hydrosulfite(SHS) technology. Alcohol water ratio is more stable, operation control is more accurate and stable.
1.3The degree of automation is improved, and the main posts are realized fully automatic and semi-automatic.
1.4Improve the structure and layout of the dryer to prevent casualties and equipment damage due to the decomposition of SHS.
1.5The waste water, waste gas and solid waste are treated thoroughly.
1.6By product, sodium sulfite, its purity is more than 96%.
1.7The recovered sodium formate from the tank/tower liquid can be reused for synthesis.
1.8Continuous improvement, more perfect technology, more perfect details.
2、 Process description
2.Batching process: put sodium formate, mother liquor and water in a certain proportion into the sodium formate preparation tank, and obtain the sodium formate suspension by mixing. Sodium metabisulfite(SMBS), liquid sulfur dioxide(SO2) and methanol are put into the SMBS preparation tank in a certain proportion, and SMBS suspension is obtained by mixing.
2.2Synthesis process: add the above two kinds of suspensions to the synthesis reactor in a certain proportion, and add ethylene oxide at the same time. After the suspension is finished feeding, continue to add liquid SO2 until the reaction end point, then, we can get the SHS suspension. During the reaction, the temperature is controlled at 75-85 ℃, the pressure is at 0.15-0.25MPa, and PH 4.1-5.2. The synthetic tail gas enters the tail gas condenser, then, sulfur dioxide (SO2), methanol, methyl formate and other substances can be recovered, and the condensate is reused for synthesis. The condensed tail gas enters the tail gas absorption tower.
Na2S2O5 + 2SO2 + 2HCOONa = 2Na2S2O4 + H2O + 2CO2
2.3Drying and packaging process: SHS suspension goes into the dryer, through filtering, and washing by methanol, and then it is heated and dired by putting hot water into the jacket and coil. A certain amount of soda ash is added to dried SHS as a stabilizer. The product is packed after mixing evenly. 70-80% of the filtrated mother liquor is reused in the batching process. Washing methanol and a small part of mother liquor are sent to neutralization process to recover by-product of sodium sulfite.
2.4Neutralization process: washing methanol from drying process and a small part of mother liquor are added to neutralization reactor, and then caustic soda is added for neutralization to obtain sodium sulfite suspension. After filtration, washing and drying, the sodium sulfite suspension is packaged as a by-product. The filtrated neutralization solution is stored in the neutralization solution tank and sent to the distillation process for methanol recovery.
NaHSO3 + NaOH = Na2SO3 + H2O
2.5Distillation and sodium formate recovery process: the neutralization liquid is added into the distillation column, and the steam is used as the heat source. Methanol gas is obtained at the top of the distillation column, and methanol is obtained after condensation. Methanol is reused in batching, drying and other processes. The bottom of the column is the distillation residue. There is sodium formate in the distillation residue. After concentration, crystallization and purification, we can get solid sodium formate which purity ≥ 90%, and it is reused in the batching process. After the extraction of sodium formate, the residue contains 40-50% sodium salt and 50-60% organic matter. The residue is sent to the waste solid treatment process.
2.6Tail gas treatment process: the tail gas of each process is condensed first, then enters the tail gas washing tower, and is washed with alkali water to remove SO2 in the tail gas, and the absorption liquid is sent to the neutralization process to recover sodium sulfite. The tail gas after removing SO2 enters the waste solid burner, and the organics and peculiar smell are removed through high-temperature incineration.
SO2 + NaOH = Na2SO3 + H2O
2.7Process flow chart
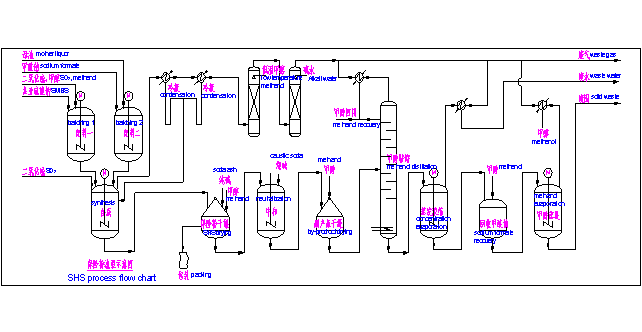
3、Product standard and consumption indexes
3.1SHS quality standard
3.2By-product sodium sulfite anhydrous quality standard
3.3SHS consumption list
4、Treatment for “3 wastes”
4.1Waste water
1)Source and composition of waste water: the waste water mainly comes from the distillation residue of the distillation process, and its general composition is as follows:
2)Waste water treatment measures: after the distillation residue is concentrated and the organic matter is separated by methanol extraction, the sodium formate is extracted and reused in SHS production. The secondary steam condensate produced by concentration is reused in neutralization process and batching process. The waste water that has not been reused will be treated by oxidation, anaerobic and aerobic treatment, and it will meat 1st grade of discharge requirements and can be discharged. The methanol extraction liquid is sent to the evaporation tank to recover the methanol, and the bottom residue after the methanol evaporation is sent to the waste solid burner.
4.2Waste gas
1)Source and composition of waste gas: the waste gas mainly comes from synthesis tail gas, dry pressing material and material transportation vent tail gas, vacuum pump tail gas. The main pollution factors of each kind of gas are SO2, CH3OH, etc. Other components are nitrogen and CO2.
2)Waste gas treatment measures: first, CH3OH, SO2, methyl formate and other substances are recovered through cold methanol absorption. The absorption liquid is reused to the batching post. Then it enters into alkali washing, which is washed with alkali water, and sodium sulfite is recovered from the neutralization process of washing liquid, and the gas after alkali washing enters into the waste liquid burner. Remove organic matter and peculiar smell through incineration. After the incineration, the tail gas is washed by alkali to remove SO2, then, gas will meet the discharge standard.
4.3Solid waste
1)Source and composition of solid waste: solid waste comes from the residue after the extraction of sodium formate. It contains 40-50% sodium salt and 50-60% organic matter. It is paste or viscous oil at room temperature.
2)Solid waste treatment measures: incineration is adopted. After incineration, we will get molten salt containing sodium sulfide and sodium carbonate and tail gas containing sulfur dioxide are obtained. After the molten salt is dissolved with water, will absorb the tail gas containing SO2. The by-product of sodium bicarbonate is obtained by the way of sulfur synthesis, concentration crystallization and centrifugation. The tail gas of incineration is absorbed by alkali liquor and then can meet discharge standard.
4.4Summary of 3 wastes after treatment:
1.1The average of product purity is more than 91%, the rate of superior product is more than 80%, and the rate of first-class products is more than 90%.
1.2The process belongs to the sixth generation of sodium hydrosulfite(SHS) technology. Alcohol water ratio is more stable, operation control is more accurate and stable.
1.3The degree of automation is improved, and the main posts are realized fully automatic and semi-automatic.
1.4Improve the structure and layout of the dryer to prevent casualties and equipment damage due to the decomposition of SHS.
1.5The waste water, waste gas and solid waste are treated thoroughly.
1.6By product, sodium sulfite, its purity is more than 96%.
1.7The recovered sodium formate from the tank/tower liquid can be reused for synthesis.
1.8Continuous improvement, more perfect technology, more perfect details.
2、 Process description
2.Batching process: put sodium formate, mother liquor and water in a certain proportion into the sodium formate preparation tank, and obtain the sodium formate suspension by mixing. Sodium metabisulfite(SMBS), liquid sulfur dioxide(SO2) and methanol are put into the SMBS preparation tank in a certain proportion, and SMBS suspension is obtained by mixing.
2.2Synthesis process: add the above two kinds of suspensions to the synthesis reactor in a certain proportion, and add ethylene oxide at the same time. After the suspension is finished feeding, continue to add liquid SO2 until the reaction end point, then, we can get the SHS suspension. During the reaction, the temperature is controlled at 75-85 ℃, the pressure is at 0.15-0.25MPa, and PH 4.1-5.2. The synthetic tail gas enters the tail gas condenser, then, sulfur dioxide (SO2), methanol, methyl formate and other substances can be recovered, and the condensate is reused for synthesis. The condensed tail gas enters the tail gas absorption tower.
Na2S2O5 + 2SO2 + 2HCOONa = 2Na2S2O4 + H2O + 2CO2
2.3Drying and packaging process: SHS suspension goes into the dryer, through filtering, and washing by methanol, and then it is heated and dired by putting hot water into the jacket and coil. A certain amount of soda ash is added to dried SHS as a stabilizer. The product is packed after mixing evenly. 70-80% of the filtrated mother liquor is reused in the batching process. Washing methanol and a small part of mother liquor are sent to neutralization process to recover by-product of sodium sulfite.
2.4Neutralization process: washing methanol from drying process and a small part of mother liquor are added to neutralization reactor, and then caustic soda is added for neutralization to obtain sodium sulfite suspension. After filtration, washing and drying, the sodium sulfite suspension is packaged as a by-product. The filtrated neutralization solution is stored in the neutralization solution tank and sent to the distillation process for methanol recovery.
NaHSO3 + NaOH = Na2SO3 + H2O
2.5Distillation and sodium formate recovery process: the neutralization liquid is added into the distillation column, and the steam is used as the heat source. Methanol gas is obtained at the top of the distillation column, and methanol is obtained after condensation. Methanol is reused in batching, drying and other processes. The bottom of the column is the distillation residue. There is sodium formate in the distillation residue. After concentration, crystallization and purification, we can get solid sodium formate which purity ≥ 90%, and it is reused in the batching process. After the extraction of sodium formate, the residue contains 40-50% sodium salt and 50-60% organic matter. The residue is sent to the waste solid treatment process.
2.6Tail gas treatment process: the tail gas of each process is condensed first, then enters the tail gas washing tower, and is washed with alkali water to remove SO2 in the tail gas, and the absorption liquid is sent to the neutralization process to recover sodium sulfite. The tail gas after removing SO2 enters the waste solid burner, and the organics and peculiar smell are removed through high-temperature incineration.
SO2 + NaOH = Na2SO3 + H2O
2.7Process flow chart
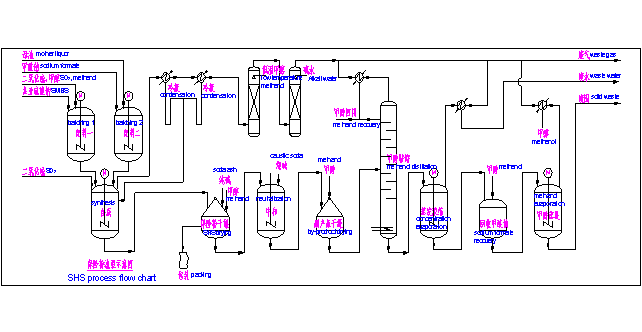
3.1SHS quality standard
item | Index | ||
superior product | 1st grade product | qualified product | |
appearance | white crystalline powder | ||
%; SHS weight % | ≥90.0% | ≥88.0% | ≥85.0% |
smell | slightly SO2 smell | ||
dissolved state | clear after dissolving in neutral formaldehyde |
Item | Unit | Index |
sodium sulfite purity | % | ≥96 |
No. | Item | Unit | Consumption quota |
1 | sodium formate (reduce moisture) | t | 0.47 |
2 | liquid SO2 | t | 0.48 |
3 | SMBS | t | 0.45 |
4 | caustic soda (reduce moisture) | t | 0.08 |
5 | methanol | t | 0.03 |
7 | soda ash | t | 0.04 |
8 | ethylene oxide | t | 0.022 |
9 | power | kwh | 260 |
10 | steam 0.8MPa | t | 1.8 |
11 | tap water | t | 5 |
4.1Waste water
1)Source and composition of waste water: the waste water mainly comes from the distillation residue of the distillation process, and its general composition is as follows:
No. | Composition | Purity |
1 | water | 84% |
2 | HCOONa | 12% |
3 | Na2SO3 | 1% |
4 | NaCO3 | 1% |
5 | Na2S2O3 | 0.50% |
6 | NaCl | 0.50% |
7 | organics | 2% |
4.2Waste gas
1)Source and composition of waste gas: the waste gas mainly comes from synthesis tail gas, dry pressing material and material transportation vent tail gas, vacuum pump tail gas. The main pollution factors of each kind of gas are SO2, CH3OH, etc. Other components are nitrogen and CO2.
2)Waste gas treatment measures: first, CH3OH, SO2, methyl formate and other substances are recovered through cold methanol absorption. The absorption liquid is reused to the batching post. Then it enters into alkali washing, which is washed with alkali water, and sodium sulfite is recovered from the neutralization process of washing liquid, and the gas after alkali washing enters into the waste liquid burner. Remove organic matter and peculiar smell through incineration. After the incineration, the tail gas is washed by alkali to remove SO2, then, gas will meet the discharge standard.
4.3Solid waste
1)Source and composition of solid waste: solid waste comes from the residue after the extraction of sodium formate. It contains 40-50% sodium salt and 50-60% organic matter. It is paste or viscous oil at room temperature.
2)Solid waste treatment measures: incineration is adopted. After incineration, we will get molten salt containing sodium sulfide and sodium carbonate and tail gas containing sulfur dioxide are obtained. After the molten salt is dissolved with water, will absorb the tail gas containing SO2. The by-product of sodium bicarbonate is obtained by the way of sulfur synthesis, concentration crystallization and centrifugation. The tail gas of incineration is absorbed by alkali liquor and then can meet discharge standard.
4.4Summary of 3 wastes after treatment:
|
discharge point | discharge flow | Index |
waste water | waste water treatment device |
600-1000kg/T 600-1000kg/t SHS |
1st grade discharge standard |
waste gas | solid waste burner chimney |
850Nm3/T 850Nm3/t SHS |
SO2:30mg/m3 |
solid waste | solid waste treatment process |
2-5kg/T 2-5kg/t SHS |
Mainly sodium chloride |